In the last installment of The Journey of Cotton, we reviewed the different finishes that can be applied to cotton. After moving through our multi-step purification process, purified cotton leaves Barnhardt’s facility in compact, 500-pound bales of fiber. We ship these bales to nonwoven roll goods manufacturers around the world. Manufacturers utilize several platforms of nonwoven fabric formations to produce cotton nonwoven fabrics. They can use purified cotton alone or blended with any other types of natural or synthetic staple fibers, depending on the desired fabric properties.
Today, let’s take a look some of the different techniques that manufacturers use to convert cotton into their final products.
Web Formation
Common practices among all all nonwoven fabric producers are opening the cotton fiber from the bale, fashioning the fibers into smaller tufts, and then forming a web of fibers. They can achieve this process by carding or air-laying (Rando-type machinery).
Carding
Carding is the most commonly-used method. The card will feed in the batt of fibers using a slow, sawtooth wire-covered roll to the main cylinder (which is also covered in sawtooth wire and traveling at much higher speed). The main cylinder will move the fibers very quickly past stationary plates, which are also wire-covered. The gap between the cylinder and stationary plates, where the carding action takes place, is very tight, as close as one-hundredth of an inch.
This process opens the fibers and individualizes them, combing them so the length of each fiber is oriented in the same direction the cylinder is moving (machine direction). At the exit, a slower wire-covered roll removes the fibers in the form of a web from the main cylinder and deposits the web on a conveyor that leads to bonding. Because the fibers are all oriented in the machine direction, fabric made of card webs is thus stronger in the machine direction.
Air-laying or Dry-laying
In the air-laid (also known as dry-laid) process, the steps are much the same as carding, with wire-covered rolls that open and orient the fiber. However instead of using a wire-covered roll to remove the fibers,a wall of air blows each fiber from the cylinder. The fibers and air blow onto a rotating collection drum that has negative pressure inside. Machinery pulls the air though the drum, collecting the fibers on the outside of the drum and removing them as a web. Due to the air turbulence, the fibers are no longer in any ordered orientation (randomized). This web, when bonded, will produce fabrics with equal strength properties in all directions.
Bonding Methods
Manufacturers produce nonwoven fabrics by bonding the carded or air-laid fiber webs together by mechanical, thermal or chemical means. Next, let’s take a look at the bonding methods for purified cotton. Manufacturers may use 100 percent cotton fibers or blends of cotton and other fibers for all of the following bonding methods, with the exception of thermal bonding, which requires thermoplastic fibers.
Hydroentangling or Spunlace
Hydroentanglement, also known as spunlace, is a process where high-pressure water jets strike the fiber web, causing the fibers to mechanically entangle with each other. This entanglement gives the fabric its strength. Hydroentangled fabrics are the most “textile-like” of all nonwovens. Since only water is used to bond these fabrics, they are very soft, drapable, and pure.
Needle-punching
Needle-punched fabrics result from having thousands of barbed needles driven through the fiber web. The barbs on the needles grab fibers from the top of the web and push them through the rest of the web. When the needle extracts itself, the punched fibers are left in place. This fiber entanglement gives needle-punched fabrics their strength. Manufacturers can produced needle-punched fabrics in very heavy weights.
Chemical Bonding
Chemically-bonded fabrics feature a web of fibers applied with sticky chemicals.. Manufacturers apply chemicals via padding, spray, or foam into the web. After applying the chemical binders, they normally heat the web, and the fibers become glued together where they intersect, providing fabric strength.
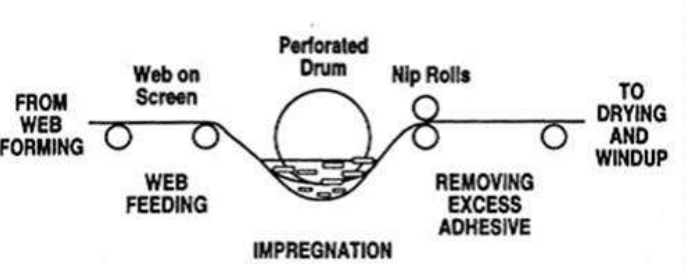
Thermal Bonding
Manufacturers produce some fabrics by using heat to melt thermoplastic fibers (polypropylene, polyethylene). This process is known as thermal bonding. The thermoplastic fibers melt together where they intersect, yielding fabric strength. Since cotton fibers do not melt, they must be blended with thermoplastic fibers that do melt to produce these thermal-bonded fabrics. Manufacturers use a couple of different methods to achieve thermal bonding:
Calendaring
The fiber web is passed between two heated rolls that melt the fibers together. This method produces a thin fabric due to the weight and pressure of the rolls.
Through-Air
Through-air bonding produces a lofty fabric. To produce these fabrics, the fiber web passes through an oven, where hot air is pulled through the web to melt the fibers together at their intersection points. Since there is no pressure, the fabric retains the loft of the web.
Post-Fabric Treatment
Any of the nonwoven fabrics produced by the various bonding methods discussed can be treated with other chemicals to impart any desired fabric properties. Just to name a couple of examples, manufacturers may treat fabrics to make them flame-retardant or feature a water-repellent finish.
Conversion
During their last processing stop, Nonwoven fabrics then convert into final products. Conversion can be as simple as slitting and cutting the fabric, as with a a wipe product, where the fabric would be cut to size, folded, and packaged. Sometimes, manufacturers may combine certain nonwovens with other nonwoven fabrics or components to create complex products such as a disposable baby diapers, which can contain 15 or more separate components!
Please visit our blog for a range of articles on nonwoven fabrics and customization techniques. To learn more about how Barnhardt can meet your needs for nonwoven fabrics, contact us today.