Journey to Zero
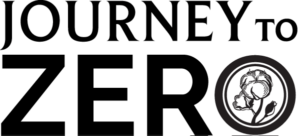
The Journey to Zero is an approach to change our safety culture from being reactive to proactive.
We use the word journey because changing the safety culture isn’t instantaneous but a process of placing emphasis on proactively identifying and eliminating unsafe acts and unsafe conditions rather than responding to them after someone is injured.
The Heinrich Triangle illustrates a reactive safety culture. Basically, when unsafe acts go uncorrected, you can expect near misses to occur, then minor injuries to occur, then major injuries, and possibly death. Unfortunately, some companies only act when someone is severely injured. Then they investigate and implement countermeasures to prevent a similar incident. It’s a “roll of the dice” mentality, hoping no one gets hurt.
The Journey to Zero takes the Heinrich Triangle and reverses it to be positive.
At the bottom of the triangle are Behavior Safety Interactions. BSIs are opportunities to change unsafe behavior and to recognize safe behavior.
While we require managers and supervisors to have BSI conversations with their associates, we encourage all associates to be brothers/sisters to each other by engaging in BSI conversations.
The next level is “Good Catches,” which are unsafe conditions/hazards or suggestions to improve safety.
They are called “Good Catches” because corrective actions were implemented to reduce or eliminate the risk associated with those hazards, or the suggestion was implemented, improving overall safety.
Next, we investigate all near misses, property damages, and injuries, no matter how minor, and then implement corrective actions immediately. In this way, we can reduce the probability of severe injuries occurring.
Associate engagement is essential on our Journey to Zero
- Associates are empowered to stop work for unsafe conditions.
- Everyone is encouraged to join one of the associate-led safety teams.
- Associates are encouraged to have BSI conversations with each other.
- Associates are encouraged to submit “good catches.”
- Associates are encouraged to perform safety audits. Audits are opportunities to have BSI conversations with coworkers and to identify “good catches.”
- Associates are encouraged to lead safety talks and safety training.
Ultimately, associates become subject matter experts in safety and proactively stop unsafe acts and eliminate hazards, resulting in zero.
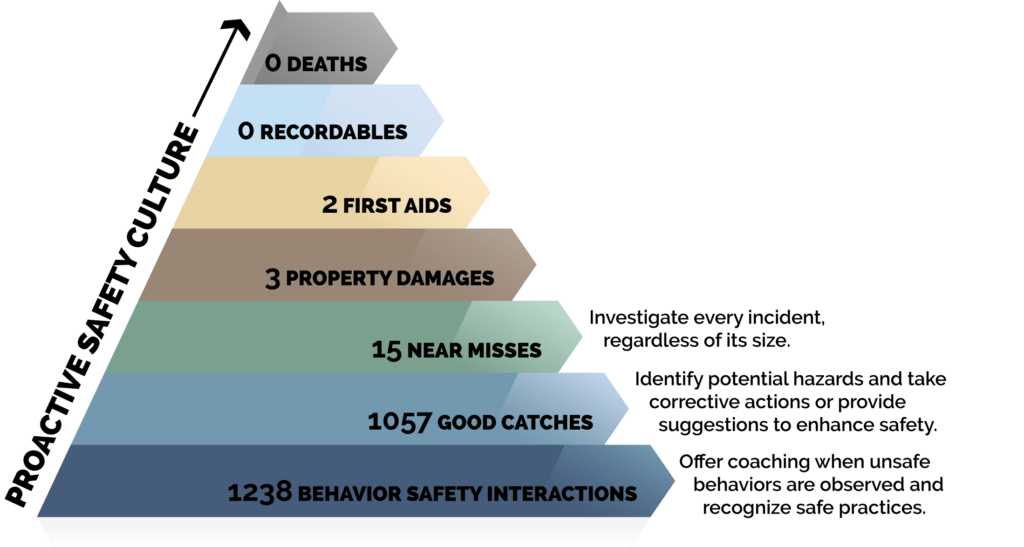